Blister Packaging: Environment, Sustainability and Materials
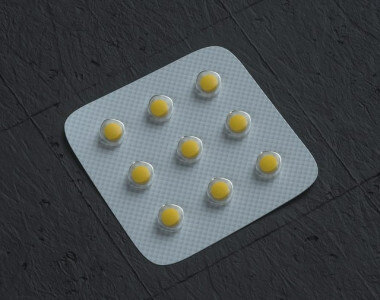
Most people do not think about pharmaceutical packaging, but it has a huge impact on the safety and effectiveness of the medication it houses. Blister packaging serves not only as a practical method of medication containment but also plays a pivotal role in safeguarding the environment.
This article delves into the intricacies of blister packaging, focusing on its environmental impact, sustainability, and the materials involved in its construction. These insights will help you understand how such packaging preserves the integrity of pharmaceutical products while addressing critical environmental concerns.
Read more:
- Future Innovations in Blister Packaging
- How Pharmaceutical Blister Packs Protect Medicines & Enhance Patient Safety
Blister Pack Materials
Blister packs utilize various materials, each chosen for specific properties that enhance the protection of the medication:
- PVC (Polyvinyl Chloride): Commonly used for its flexibility and ease of forming.
- PVDC (Polyvinylidene Chloride): Added to PVC to increase moisture and oxygen barrier properties.
- Aluminum: Often used for the lidding foil, providing a complete barrier against light, moisture, and gases.
The manufacturing process of blister packs involves several critical steps to ensure the optimal protection and presentation of pharmaceutical products:
- Forming the base web: The chosen material (typically PVC or PVC/PVDC) is heated and formed into pockets.
- Filling the pockets: Each blister is accurately filled with the respective medication.
- Sealing with lidding material: A lidding material, usually aluminum foil, is sealed over the base web, enclosing the medication.
- Cutting and finishing: The web is cut into individual blister packs and embossed or printed as needed.
Advancements in technology have significantly improved the manufacturing process of blister packs. Modern machinery allows for more precise filling and sealing, ensuring the integrity of the medication and the consistency of each dose.
Additionally, innovations in material science have led to the development of more durable and protective packaging, further enhancing the shelf-life and safety of pharmaceutical products.
Environmental Considerations in Blister Packaging
The manufacturing and disposal of blister packaging pose several environmental challenges. Although effective in protecting medications, the materials used in blister packs can have significant environmental impacts:
- Waste Generation: Blister packs often result in a considerable amount of waste due to their single-use nature.
- Resource Consumption: The production of blister packaging materials such as PVC and aluminum requires substantial resources.
- Recycling Challenges: Blister packs can be difficult to recycle due to the mix of materials used.
Considering these impacts, selecting blister packaging solutions that minimize environmental harm is crucial. Options that reduce VOC emissions are better for air quality, while compliance with solvent emissions regulations ensures lesser environmental contamination.
Additionally, choosing materials with a lower fire hazard risk enhances safety in production facilities. These eco-friendlier choices not only align with sustainability goals but also resonate with environmentally conscious consumers.
Closing Thoughts
The world of blister packaging is one where innovation meets responsibility. As we delve into the intricacies of materials like PVC and PVDC and marvel at the advancements in sealing technologies, it becomes clear that this is not just about containing medication. It’s about protecting our health and our planet simultaneously.
Companies like Colorcon are at the forefront of this delicate balancing act, ensuring that every tablet we take is not just effective but also packaged with an eye toward sustainability.
As we look to the future, the continuous evolution of blister packaging stands as a testament to the pharmaceutical industry’s commitment to both patient care and environmental stewardship – a harmony of purpose that benefits us all.