Extended Release Tablet Formulation: Challenges & Best Practices
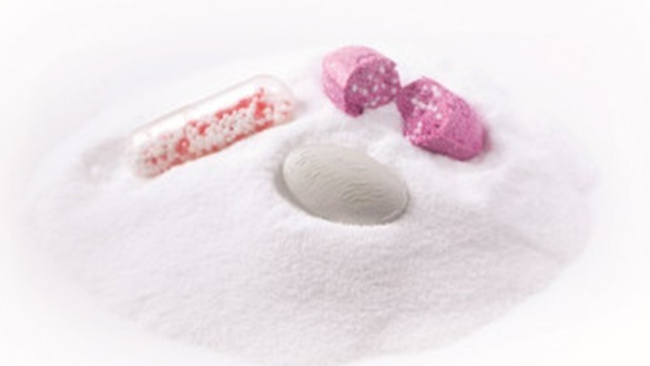
Imagine managing a chronic condition by taking just one pill every morning instead of setting reminders throughout the day. Extended-release (ER) tablets have made this reality possible for millions worldwide by providing steady medication release over time.
Today, this technology is used in medications that treat everything from hypertension to diabetes and mental health disorders. They've improved patient compliance, reduced side effects, and enhanced overall treatment efficacy.
But creating these life-changing medications is no simple task. It requires a delicate balance of scientific expertise, cutting-edge technology, and meticulous attention to detail.
What Is Extended Release Formulation?
An extended release formulation is when a tablet or capsule is designed to release a drug in a controlled manner over a prolonged period of time after the dose is consumed by the patient. These dosages usually use hydrophilic or hydrophobic matrix systems, reservoir systems, multiparticulate, and osmotic release systems.
Advantages of Extended Release Formulation
Extended release in many types of drugs is helpful for three key reasons:
- It improves patient compliance because a patient doesn’t have to remember to consume multiple pills over the course of a day.
- It reduces the "pill burden" on patients, or the negative psychological effect of taking lots of pills each day.
- It may reduce adverse side effects or even the risk of seizures by limiting the intensity of the drug after the initial dose.
Extended Release vs. Controlled Release vs. Sustained Release
Controlled release (CR) and sustained release (SR) both fall under the broader category of extended release – also known as modified release. Controlled release involves medication that maintains a constant release of the drug over a period of time. Sustained release, on the other hand, releases drug at a predetermined rate to maintain a constant drug concentration for a specific period of time with minimum side effects.
SR medication is typically available in oral dosage forms, but CR medication can be administered into the body through other means besides oral dosage.
Delayed release (DR) is another form of modified release and these oral solid dosage forms are widely used to protect the gastric mucosa from irritating actives or to protect drugs sensitive to gastric fluids. For example, a drug meant to provide treatment to the small intestines would need to not release its active ingredient until it had reached this part of the body. They are designed for use on tablets or multiparticulate solid oral dosage products, including proton pump inhibitor (PPI) applications and enteric coated aspirin, which is widely taken.
Challenges for Extended Release Tablet Formulation
We spoke with Beth Tran, Colorcon’s Global Business Manager, about the challenges pharmaceutical companies face in developing ER tablets and the best practices they employ to overcome them. She identified four primary challenges: getting the release profile right, ensuring formulation is consistent and reliable, matching innovator products, and acquiring the necessary technical expertise.
Challenge #1: The Importance of Release Profiles
One of the primary challenges in ER formulation is achieving the desired release profile. "It’s the main challenge for controlled release or any kind of extended release from a high level,” Tran says.
Release profiles are critical because they determine how the drug is released over time in the body. Manufacturers aim for either zero-order (constant release) or first-order (gradual decrease in release rate) profiles, depending on the specific drug and therapeutic goals.
Best Practice: Utilize Pre-formulated Systems
To address this challenge, Tran suggests leveraging pre-formulated systems. “We want to get more and more of our customers to start going toward our formulated systems,” she says. “The benefit there is that we've already created an optimized formulation that's consistent and will deliver those types of controlled release profiles on a consistent basis."
By using pre-formulated systems, pharmaceutical companies can benefit from proven formulations that consistently achieve desired release profiles. This approach can save time and resources in development while ensuring greater reliability in the final product.
Challenge #2: Consistency and Reliability in Formulation
Ensuring consistency in the formulation process is another big challenge. Inconsistencies in the formulation can lead to variations in drug release, potentially affecting the drug's efficacy and safety.
"Our products definitely provide solutions to consistency and reliability because they're formulated systems,” Tran says.
Best Practice: Implement Mixing/Blending Processes
To address this challenge, companies should focus on implementing robust mixing and blending processes. Tran emphasizes the importance of uniformity in the blend: by using high-quality formulated systems and paying careful attention to the mixing and blending stages, manufacturers can ensure greater consistency in their final products.
This may involve investing in advanced mixing equipment, developing standardized procedures, and implementing rigorous quality control measures throughout the production process – or working with a company like Colorcon that already has these capabilities.
Challenge #3: Matching Innovator Products
Generic drug manufacturers face an additional challenge: achieving bioequivalence with the innovator product while developing a unique formulation. This requires a lot of expertise and resources.
“We have generic companies that are trying to formulate and copy innovators,” Tran says. “They’re really trying to make sure they match exactly what innovators are doing. And that's where we would come in.”
Best Practice: Partner with Experienced Formulation Experts
To overcome this challenge, generic manufacturers should consider partnering with experienced formulation experts. Companies like Colorcon can provide valuable assistance in this area.
These partnerships can offer access to specialized knowledge, advanced technologies, and proven formulation strategies that can help generic manufacturers achieve bioequivalence more efficiently. By using external expertise, generic companies can streamline their development process and increase their chances of successfully matching innovator products.
Challenge #4: Technical Expertise Gap
Not all companies have the in-house expertise to develop complex ER formulations. Tran notes. “Sometimes there are challenges with just understanding what the technologies are for a zero-order release,” she says. “Customers just don't have that expertise. So sometimes that's the challenge as well: knowing where to find the people the right people to to direct those types of projects.”
This knowledge gap can significantly impact a company's ability to develop effective ER formulations.
Best Practice: Leverage External Expertise
To bridge the technical expertise gap, companies should take advantage of the knowledge and experience already available in the industry. As Tran suggests, this is where companies like Colorcon can play a crucial role. By partnering with experts who have deep knowledge of various ER technologies, such as osmotic pump formulations, companies can:
- Access specialized knowledge without the need for extensive in-house training
- Benefit from years of industry experience and best practices
- Stay up-to-date with the latest advancements in ER formulation technologies
- Receive guidance tailored to their specific product needs
Leveraging external expertise can significantly accelerate the development process and improve the chances of creating successful ER formulations, even for companies without extensive internal resources.
Final Thoughts
Developing extended release tablet formulations presents several challenges, from achieving desired release profiles to ensuring formulation consistency, matching innovator products, and overcoming technical expertise gaps.
By implementing best practices such as using pre-formulated systems, focusing on robust processes, and taking advantage of external expertise, pharmaceutical companies can deal with these challenges a lot more effectively.
The key to success in ER tablet formulation lies in recognizing when to seek external support. Whether you're a generic manufacturer looking to match an innovator product or a company exploring new ER technologies, contact Colorcon. Our expertise and formulated systems can support your ER tablet development efforts, helping bring your innovative treatments to patients more efficiently.